Anyone seriously interested in making knives has probably heard of air-hardening tool steel, or the A-steel family (A2 – A10). More specifically, A2 steel. It is one of the most common steels for making sharp tools like knives.
If have this question in mind “Is A2 a good knife steel” you’ve come to the right place. I decided to research this steel and answer some of the most frequently asked questions, such as: What kind of steel is it? What is its chemical composition? What is its hardness? Is it a good knife steel or rather not? So, let’s not waste time and get started!
Table of Contents
What is A2 steel?
A2 is a medium-grade air-hardening tool steel and is also known as 1.2363 steel. 1.2363 steel is a cold work steel improved based on SKD11 steel with a toughness twice as high. A2 steel is known for its good toughness (tougher than D2 or M2 steel) and has a wear resistance that is between O1 and D2 steel. It is used for punches and dies, clamping jaws, cutting tools for woodworking, tools for plastic injection, dowel pins, hammers, industrial knives, and gauges, among other applications.
History of A2 steel
A2 steel is quite old, although determining the exact year it was first available is somewhat difficult. A2 steel was developed in the early 20th century after the discovery of high-speed steel, which was first introduced in 1900.
The development of the first high-speed steel switched from manganese to chromium as the primary hardenability element, and most high-speed steels contained about 4% chromium. This high chromium content was primarily for “hardenability”, i.e. the degree of quenching required to achieve full hardness.
A steel quenched in water has low hardenability and must be quenched very quickly from its high temperature, while an “air-hardening” steel can be left in the air and harden completely. The first high-speed steel was a steel called “T1” which contained 4% chromium and 18% tungsten).
The earliest record that is of an A2 type precursor steel is from 1916, more specifically it is found in a list of brand names of current tool steels in Machinery magazine (Vol. 22, No. 6) as CYW Choice by Firth-Sterling and Vasco Choice by Vanadium Alloys Steel Company (Vasco).
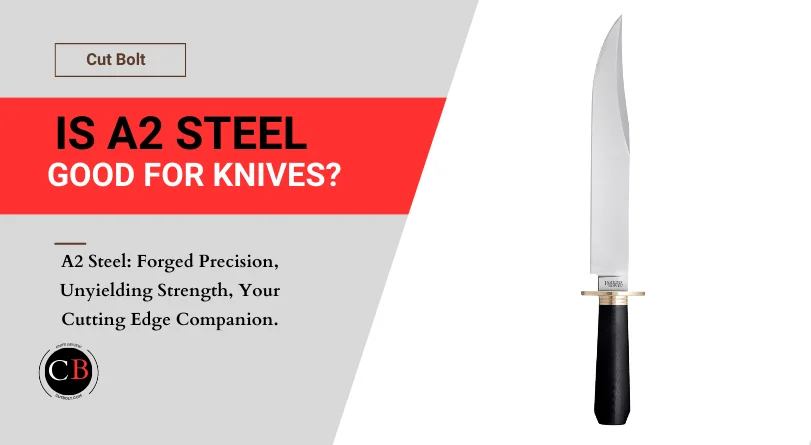
A2 steel chemical composition
Element | Portion | Effect |
Chrome | 5.5% | Improves wear resistance, heat resistance and scale resistance. It increases tensile strength as it acts as a carbide former. Use of stainless or stainless steels, as it increases corrosion resistance from a mass proportion of 12.2%. Reduction in weldability. |
Carbon | 1.05% | Increasing hardness and tensile strength. In larger quantities, increase in brittleness and reduction in forgeability and weldability. |
Copper | 0.25% | Improving weather resistance (surface oxidation). |
Manganese | 1.0% | Improves hardness and tensile strength. |
Molybdenum | 1.4% | Improves hardenability, tensile strength and weldability. Reduction in malleability and ductility. |
Nickel | 0.3% | Nickel increases tensile strength and yield strength. From 8% increase in corrosion resistance. |
Phosphorus | 0.3% | Increases tensile strength, hardness and corrosion resistance but also brittleness. |
Sulfur | 0.3% | Increases machinability but also brittleness. |
Silicon | 0.5% | Improves strength. |
Vanadium | 0.25% | Increasing hardness, increasing wear resistance and improving tempering resistance. |
The chemical composition of A2 steel is a mixture of high carbon content and chromium, which puts the focus on toughness and corrosion resistance. Under common heat treatment conditions, the retained austenite content is almost completely decomposed in the process. The toughness of A2 steel is great in cold-work forming steel. A2 steel industrial products therefore have no cracks.
Does A2 steel rust? Is A2 a stainless steel?
Yes, A2 will rust because it contains only 5.5% chromium. It gives it good rust protection but does not make it completely immune to corrosion.
To be considered rust-free, it must have a chromium content of at least 10.5 – 13% chromium dissolved in austenite or ferrite, depending on the definition (see here). A2 contains 5.5% chromium, which is not enough to be rustproof.
To be a stainless steel, its sulfur and phosphorus content (so-called iron companion) must not exceed 0.025% (see here). A2 is just above this.
What is the hardness (HRC) of A2 steel?
The Rockwell Hardness (HRC) of A2 steel typically falls in the range of 57-62 HRC (Rockwell C scale) when properly heat-treated. This level of hardness makes A2 steel suitable for a variety of applications, including cutting tools, knives, and other high-impact applications where hardness and edge retention are important.
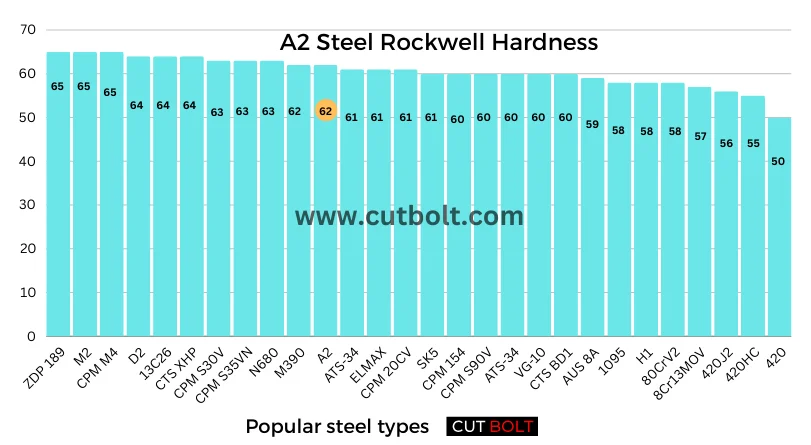
Properties of A2 steel
According to the chemical composition and hardness of A2, it offers:
- Edge retention: A2 steel has a chromium content significantly too low (5.5%) to pass as stainless or high-grade steel, but it is enough for good cut resistance.
- Corrosion resistance: A2 offers good corrosion resistance, but not the best compared to other carbon steels.
- Wear resistance: A2 can achieve high hardness, which makes it very wear resistant.
- Sharpness: Even though A2 is a hard/tough steel, it is easy to sharpen/grind due to the low chromium carbide content.
- Toughness: A2 steel offers good toughness, which is in good balance with its wear resistance. But it is not the best compared to other alloys with lower wear resistance and higher toughness (simple rule: the harder the steel, the lower its toughness).
Related: Is CPM 3V steel worth the money?
My opinion: Is A2 a good knife steel?
In my opinion, A2 is a good knife steel. It offers a good balance between hardness, wear resistance, toughness and corrosion resistance. This makes it a great steel for outdoor knives, hiking and camping, especially since it is quite easy to sharpen, plus it is relatively inexpensive.
It is well suited for outdoor and combat knives due to its high toughness, which allows applications such as “batoning” – splitting wood with a knife and a club. That said, an A2 steel knife still needs a bit of care here and there, as the chrome content provides some protection against corrosion, but the steel still rusts.
Clean after use and a drop of oil here and there and you’re on the safe side.
A2 Steel equivalents
A2 offers a combination of toughness and wear resistance similar to M2 tool steel. Both have good edge retention, great wear resistance, good toughness (M2 is better in toughness), and good corrosion resistance. D2 is also quite close to A2. D2 has the same properties but offers better corrosion resistance with slightly lower toughness.
A2 steel compared with similar steel
Here is a comparison between A2 and its close-performing steels:
A2 vs. D2 steel
Criteria | A2 | D2 |
Edge retention | 6/10 | 7/10 |
Simplicity of sharpening | 4/10 | 3/10 |
Corrosion resistance | 5/10 | 4/10 |
Toughness | 8/10 | 6/10 |
As you can see, A2 and D2 are very close. D2 holds a slightly higher edge, but A2 is a little easier to sharpen, significantly tougher and is slightly more corrosion-resistant than D2.
A2 vs O1 steel
Criteria | A2 | O1 |
Edge retention | 6/10 | 6/10 |
Simplicity of sharpening | 4/10 | 5/10 |
Corrosion resistance | 5/10 | 3/10 |
Toughness | 8/10 | 8/10 |
O1 also differs only marginally from A2 – A2 is slightly easier to sharpen and more corrosion-resistant than O1. Susceptibility to rust is the main problem with O1.
Conclusion: is A2 steel good for knives?
I recommend A2 steel for knife making. It is inexpensive, easy to work with, and well-suited for all outdoor activities where toughness and robustness are important.
However, you have to keep in mind that it is not rust-proof and requires some care in the form of cleaning after use and a drop of oil now and then.