It is from the 440 family (440 A, B, C and less commonly: F) that contains various other metals with different properties. All 440 steels are considered 100% rustproof, but 440A, which contains the lowest amount within the family, has the highest corrosion resistance.
But is 440A good knife steel? Let’s look into the properties and characteristics of this steel to determine its suitability for knives.
Table of Contents
What is 440A steel?
440A steel is a high-carbon stainless steel often used in knife blades. It belongs to the 440 series of steels which also includes 440B and 440C. 440A steel is known for its corrosion resistance and excellent wear resistance. It contains relatively high amounts of carbon, chromium, and some amount of manganese, making it a decent option for knife blades.
However, compared to 440B and 440C, 440A has lower hardness and edge retention capabilities. Nonetheless, it is considered a good all-around steel for budget-friendly knives.
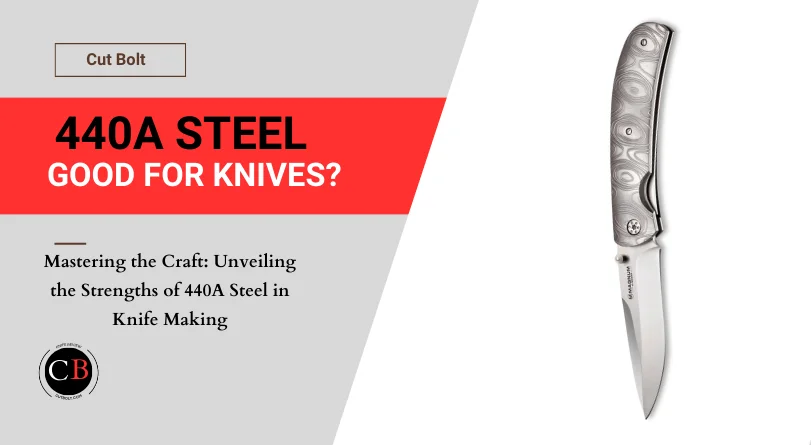
How good is 440A compared to other steels?
Compared to other steels in the 440 family (e.g. 440B and 440C), 440A has a slightly lower carbon content, which makes it somewhat softer. This means that it can be easily sharpened and (machined). Compared to stainless steel, 440A is one of the most common steels for inexpensive knife blades because it is relatively inexpensive compared to higher-grade steels. Many exhibition and replica weapons are made from 440A for this reason.
However, there are also quite a few high-end knives that use 440A, as it can be heated very high to achieve higher hardness values.
Sure there are cheaper 440A knives but that is largely due to the quality of the other components of the knife (handle, locks, etc) and the brand position of the manufacturer.
In some cases, price and stain resistance are the major selling points of this metal. In addition to its use for exhibition knives and swords, it is also a preferred choice for diver’s knives – salt water has a low corrosive effect on it.
Chemical composition of 440A
Element | Portion | Effect |
Chrome | 18.0% | Improves wear resistance, heat resistance and scale resistance. It increases tensile strength because it acts as a carbide former. Use of rust-proof or stainless steel, as it increases corrosion resistance from a mass proportion of 12.2%. Reduction in weldability. |
Carbon | 0.75% | Increasing hardness and tensile strength. In larger quantities, increase in brittleness and reduction in forgeability and weldability. |
Manganese | 0.75% | Improves hardness and tensile strength. |
Molybdenum | 0.09% | Improves hardenability, tensile strength and weldability. Reduction in forgeability and ductility. |
Nickel | 0.6% | Nickel increases tensile strength and yield strength. From 8% increase in corrosion resistance. |
Phosphorus | 0.04% | Increases tensile strength, hardness and corrosion resistance but also brittleness. |
Sulfur | 0.03% | Increases machinability but also brittleness. |
Silicon | 0.1% | Improves strength. |
The hardness of 440A steel
The Rockwell Hardness of 440A steel typically falls within the range of 55-58 HRC (Rockwell C scale). A Rockwell Hardness in the 55-58 range generally indicates a good compromise between edge retention and ease of sharpening.
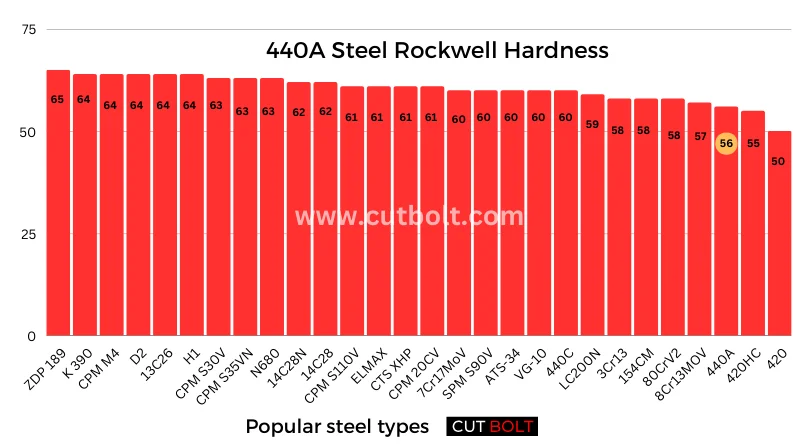
Keep in mind that knives with higher hardness may hold an edge better but can be more challenging to sharpen, while knives with lower hardness may be easier to sharpen but might require more frequent maintenance.
How 440A steel is made
To temper 440A (heat it and then let it cool slowly), heat it to 850-900°C and then cool it slowly in a furnace to about 600°C. It is then allowed to cool completely outside the furnace. Hardening is done at 1010-1065°C, cooling should be done in air or heated oil. Immediately after hardening it should be tempered at 150-370°C. Lower temperatures during tempering result in a harder final product.
Tempering above 370°C will compromise the impact resistance of the blade. However, tempering in the 590-675°C range increases impact resistance. However, the hardness must be reduced.
Comparison of alloys of steel grades 440A, 440B and 440C:
Steel designation | Carbon (C) | Chrome (Cr) | Molybdenum (Mo) | Silicon (Si) | Manganese (Mn) |
440A | 0.7 % | 14 % – 16 % | 0.8 % | 1 % | 1 % |
440B | 0.9 % | 17 % – 19 % | 0.9 % | 1 % | 1 % |
440C | 1.1 % | 16 % – 18 % | 0.6 % | 1 % | 1 % |
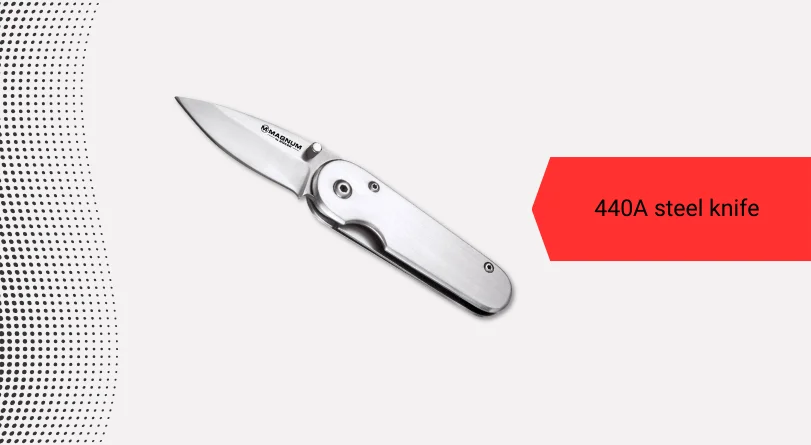
Check the 440A steel datasheet for a better understanding and find out “Is 440A good knife steel”?
Pros and Cons of 440A steel
440A steel advantages
440A stainless steel has certain advantages that make it a popular choice for knife blades and other cutting tools. Here are some of the advantages of 440A steel:
- Corrosion Resistance: 440A steel offers good corrosion resistance, making it suitable for use in environments where exposure to moisture, humidity, and other corrosive elements is common. This property helps prevent rust and staining on the blade.
- Affordability: Compared to higher-end stainless steels, 440A is more affordable. This makes knives made from 440A steel a cost-effective choice for those who want a decent level of performance without breaking the bank.
- Easy to Sharpen: 440A steel is relatively easy to sharpen. It can be honed to a fine edge, and maintenance of the blade edge is more straightforward compared to harder steels.
- Good Toughness: 440A steel exhibits good toughness, which is the ability to withstand impact and resist chipping. This characteristic is important for knives that may be subjected to heavy use or abusive conditions.
- Versatility: The balanced properties of 440A steel, including corrosion resistance, edge retention, and ease of sharpening, make it a versatile choice for a variety of cutting tasks. It is commonly used in entry-level or budget-friendly knives.
While 440A steel has these advantages, it’s important to note that it’s not the highest-performing steel available. There are higher-end stainless steels with better edge retention and other properties. The choice of steel depends on the specific needs and preferences of the user, as well as the intended use of the knife.
Disadvantages of 440A steel
Although 440A steel is outstanding in terms of cost and stain resistance, it is not as good in terms of wear resistance. Replica weapons do not have to withstand use or forces, so it is a logical choice for these items. I wouldn’t use a 440A steel knife to pry something substantial, and certainly not a folding knife. The pivot/joint is the weak point of even the best knives.
However, 440A steel should have sufficient wear resistance for light daily use in camping, outdoor, and kitchen applications.
You certainly wouldn’t make a survival knife or a scalpel for surgeons out of 440A steel. However, it is well suited for areas where rust resistance is a priority, as is the case with diving knives. Diver’s knives are not in continuous use, so wear resistance is not a major concern. However, diving knives must remain rust-free in corrosive environments.
Related: 4034 steel for knife making
Conclusion: Is 440A A Good Knife Steel
440A steel is a good choice when cost and stain resistance are primary concerns. If edge retention or the general sturdiness of the knife is a priority, another metal should be chosen. It is excellent for display pieces or as a tool for light use. Generally speaking, 440A is suitable for all kinds of applications in all kinds of situations except in extreme and most extreme conditions. Many knives with 440A steel fall in the price range of under 100 dollars, and many good knives even under 50 dollars.
Attention: with this I am not saying that 440A is a bad material.
What I am saying is that interestingly, both 440A and AUS-8 are found at the lower end of the price range for most knives. There is a reason for this.